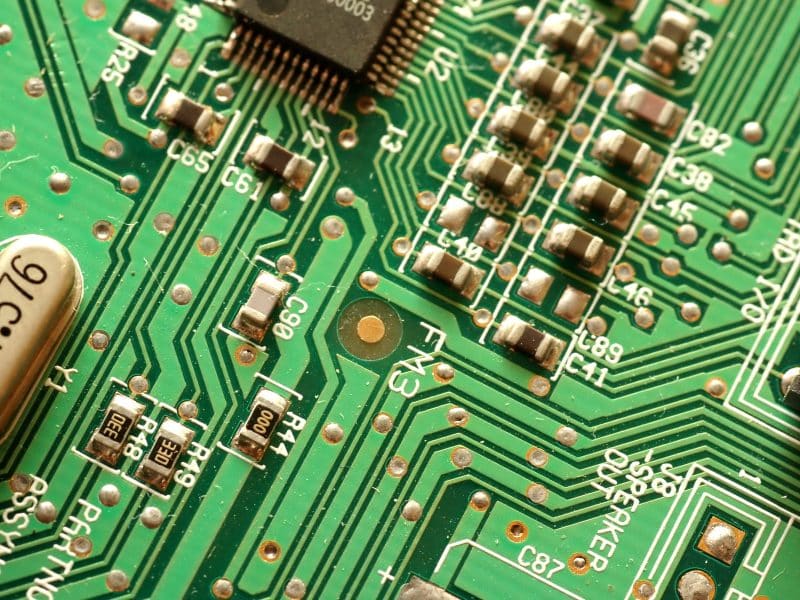
What if your next electronic device is deployed in an area exposed to high voltages or static electricity? In such scenarios, how well-prepared is your system to handle the threat of ESD? Determining a system’s vulnerability to ESD through rigorous testing methods and simulation is crucial.
Additionally, incorporating protective components can differentiate between a robust device and one that fails under high-voltage pulses. In circuit board design, ensuring your system can withstand these challenges is not just important—it’s essential for reliability and longevity.
This phenomenon can be highly harmful to electronic components, causing immediate damage or latent failures that reduce the reliability and longevity of electronic devices.
Protecting against ESD is essential in PCB manufacturing to ensure the stability and performance of the final products.
This blog delves into the importance of ESD protection, key measures to mitigate its effects, and the testing methods used to ensure robust ESD control in PCB manufacturing.
Understanding ESD and Its Impact in PCB Manufacturing
Electrostatic discharge is the sudden and transient release of static electricity. This occurs when two materials with different electrical potentials come into contact and subsequently separate, resulting in a charge imbalance. The resulting discharge can generate a high voltage, potentially damaging sensitive electronic components. ESD is a common issue in environments where electronic manufacturing occurs, as even small amounts of static electricity can lead to significant problems.
And with increasing demand for electronic devices, market trends underscore the importance of adequate ESD protection. The global market for ESD protection devices is expected to expand at a CAGR of 4.1% from 2023 to 2033, reaching 3,965.5 million by 2033.
This growth highlights the increasing recognition of ESD protection as a critical component of electronic device manufacturing, driving innovations and improvements in ESD control measures.
The impact of ESD on PCBs can be devastating. It can cause immediate failures during circuit board design or lead to latent defects that manifest later, often after the product has been deployed. Sourcing electronic components resistant to ESD is crucial for preventing such issues. These failures can include short circuits, damage to semiconductor materials, and the breakdown of dielectric layers.
Over time, repeated exposure to ESD can degrade a PCB’s performance, leading to reduced reliability and a higher likelihood of failure in the field. ESD is a significant concern for manufacturers, who must ensure that their products meet high quality and durability standards.
To mitigate these risks, the circuit board design must incorporate ESD protection from the outset. Sourcing electronic components that offer robust ESD protection can further enhance the durability of the final product.
ESD damage may not be immediately apparent but can lead to intermittent failures in electronic devices, frustrating consumers and damaging the manufacturer’s reputation. These examples highlight the importance of implementing effective ESD control measures throughout manufacturing.
Implementing comprehensive ESD protection measures right from the circuit board design phase is crucial to protecting the integrity of electronic devices and ensuring long-term reliability.
ESD Protection Measures in PCB Manufacturing
Design Considerations
One of the most effective ways to protect against ESD is to incorporate ESD protection features while designing electronic products. This can include using ground planes, which help dissipate static charges, sourcing electronic components with features that can further enhance the resilience of your circuit board design, and strategically placing components to minimise the risk of ESD exposure.
Additionally, designers can use protective devices such as transient voltage suppression (TVS) diodes designed to clamp voltage spikes caused by ESD events, thereby protecting sensitive components from damage. Proper layout and routing strategies are also essential, as they can help to reduce the risk of ESD by minimising the length of conductive traces and isolating sensitive areas of the board.
Material Selection
The materials used in PCB manufacturing play a crucial role in ESD protection. Using ESD-resistant materials, such as conductive inks and films, can help reduce the risk of ESD damage. These materials are designed to dissipate static charges before they can harm components. Coatings and encapsulants can also be applied to the PCB surface to protect against ESD. These materials are often used with other ESD control measures to create a comprehensive protection strategy.
Handling Procedures
Proper handling procedures are essential for minimising the risk of ESD during PCB manufacturing. This includes training staff on ESD awareness and best practices, such as using grounded wrist straps, antistatic mats, and ESD-safe clothing.
Workers should also be trained to handle sensitive components carefully, avoid unnecessary contact, and ensure that all equipment is properly grounded. Implementing these procedures can help prevent ESD events and ensure that components remain safe throughout manufacturing.
Testing Methods for ESD Protection
Effective testing methods for ESD protection are crucial in safeguarding the integrity of PCBs during manufacturing.
Let’s discuss the various testing methods used at different stages of the manufacturing process to ensure comprehensive ESD protection.
Pre-Manufacturing Testing
Testing for ESD protection begins during the design phase. Simulation tools are often used to assess the effectiveness of ESD protection features before manufacturing begins. These tools can model the effects of ESD events on the PCB and identify potential vulnerabilities in the design.
By identifying and addressing these issues early in sourcing electronic components, manufacturers can reduce the risk of ESD-related failures and ensure that their products meet the required standards for ESD protection.
In-Line Testing
In-line testing is essential to PCB manufacturing, allowing manufacturers to monitor ESD protection in real-time. This testing is usually done at several stages of the production process, from component assembly to final inspection.
In-line testing methods include using ESD protection devices, which generate controlled ESD events to test the robustness of ESD protection measures.
Continuous monitoring and adjustments are often necessary to protect the PCB throughout manufacturing.
Post-Manufacturing Testing
Once the PCB has been manufactured, post-manufacturing testing methods are conducted to ensure that it meets the required standards for ESD protection. This testing methods typically involves subjecting the PCB to controlled ESD events and measuring its response.
Common testing methods standards include the IEC 61000-4-2 standard, which specifies the test levels and procedures for evaluating ESD protection. Manufacturers can conduct these tests to identify any remaining vulnerabilities and take corrective action before deploying the PCB.
Best Practices for ESD Control
Creating an ESD-Controlled Environment
Creating an ESD-controlled environment is one of the most effective ways to protect against ESD in PCB manufacturing. This involves setting up ESD-safe workstations and facilities designed to minimise the risk of static buildup and discharge. ESD-safe workstations typically include grounded surfaces, antistatic mats, and ESD-safe tools and equipment.
Additionally, using grounding and shielding techniques can further reduce the risk of ESD by ensuring that all surfaces and equipment are properly grounded.
Implementing ESD Control Programs
Developing and maintaining ESD control programs is essential for ensuring that ESD protection measures are consistently applied and practical. These programs typically include guidelines for ESD-safe handling procedures, equipment maintenance, and employee training, all of which are crucial when considering circuit board design and sourcing electronic components resistant to ESD.
Regular audits and updates to the ESD control program are necessary to ensure it remains practical and current with the latest industry standards and best practices.
A study by Western Electric in 1983 demonstrated that an ESD program could effectively mitigate device failures, with reductions of up to 75% observed at one of their facilities.
By integrating circuit board design that prioritizes ESD protection and sourcing electronic components with robust ESD-resistant features, manufacturers may reduce the risk of ESD-related failures while ensuring their products satisfy the highest quality and reliability standards.
Conclusion
ESD is a significant concern in PCB manufacturing, with the potential to cause immediate or latent damage to electronic components. Implementing effective ESD control measures is essential for protecting the stability and reliability of PCBLOOP manufacturing processes.
As technology continues to advance, new challenges and opportunities will arise in the field of ESD protection. Emerging trends, such as the increasing miniaturisation of electronic components, will require new approaches to ESD control.
At the same time, advancements in materials science and testing methods will provide manufacturers with more effective tools for protecting their products against ESD.